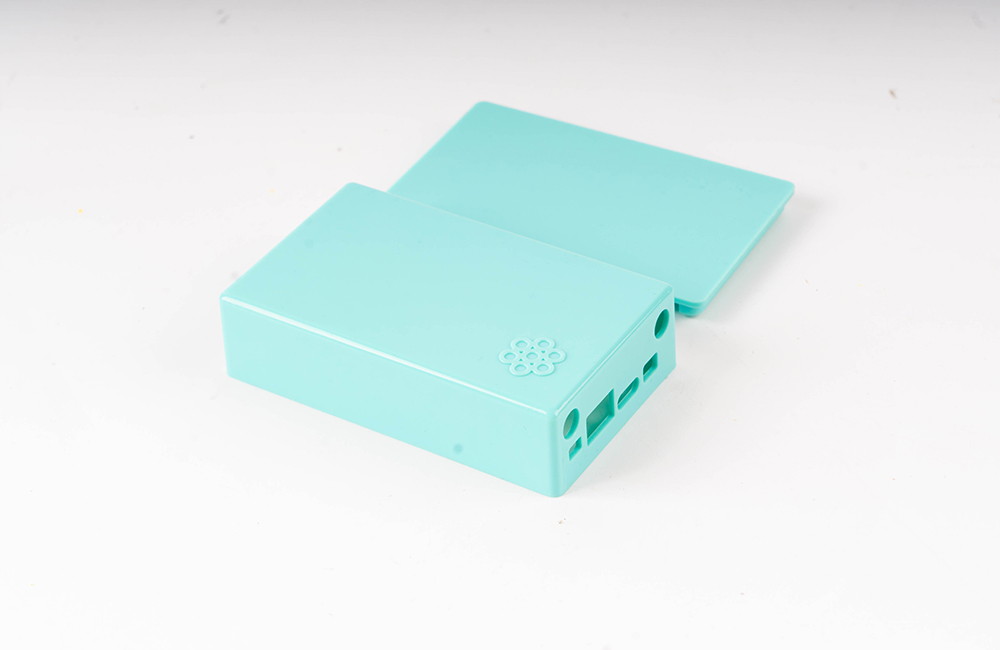
行業(yè)/分類(lèi):其他手板模型加工
加工方式: 注塑 使用材料: 塑料
最小精度: 0.1,mm 生產(chǎn)周期: 2~7天
產(chǎn)品尺寸: 15cm*10cm*5cm
后處理: 噴油
注塑加工電子設備外殼手板模型是一個(gè)將設計概念實(shí)體化、驗證產(chǎn)品設計可行性以及測試功能的重要環(huán)節。以下是關(guān)于這一過(guò)程的詳細解析:
一、注塑加工電子設備外殼手板模型的定義與目的
定義
注塑加工電子設備外殼手板模型是通過(guò)注塑工藝制作的電子設備外殼的樣品。注塑工藝是一種將熱塑性塑料或熱固性塑料加熱至熔融狀態(tài),然后注入模具型腔,經(jīng)過(guò)冷卻固化后得到與模具型腔形狀一致的塑料制品的加工方法。
手板模型則是在新產(chǎn)品開(kāi)發(fā)階段,根據設計圖紙制作出的實(shí)物模型,主要用于檢驗產(chǎn)品的外觀(guān)、結構和功能等方面的可行性。
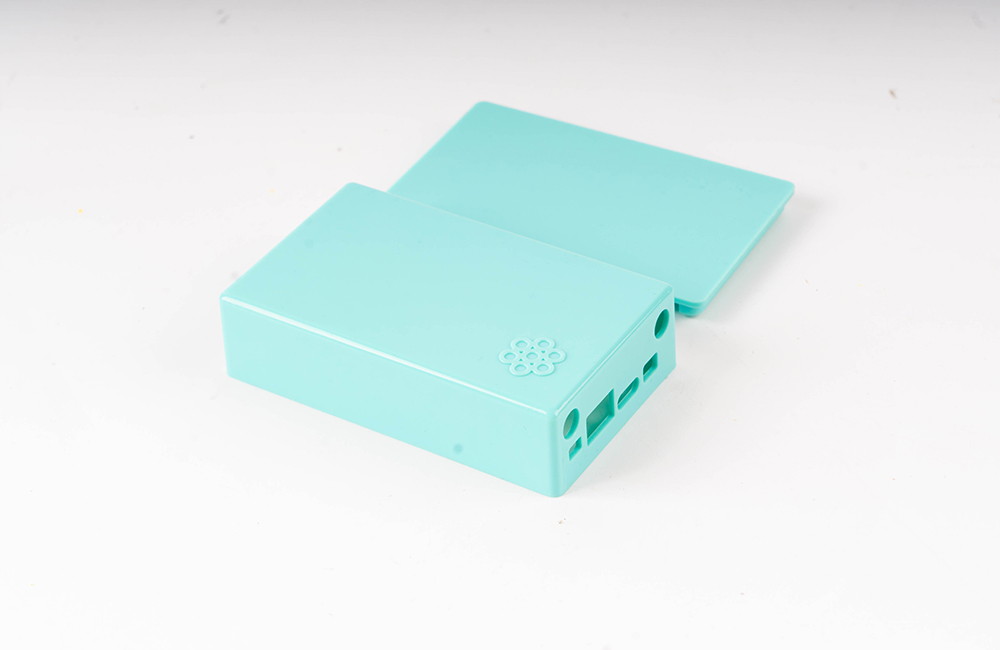
目的
驗證外觀(guān)設計:通過(guò)制作手板模型,可以直觀(guān)地展示電子設備外殼的外觀(guān)造型、顏色搭配和表面質(zhì)感等,讓設計師和客戶(hù)能夠實(shí)際感受產(chǎn)品的整體外觀(guān)效果,及時(shí)發(fā)現并修改外觀(guān)設計上的不足之處。
檢驗結構設計:檢查外殼的手板模型的結構是否合理,包括卡扣、按鍵、接口、散熱孔等部件的位置和尺寸是否合適,各部件之間的裝配關(guān)系是否緊密,以及是否存在干涉現象等,確保產(chǎn)品在組裝和使用過(guò)程中能夠正常運行。
測試功能性能:對手板模型進(jìn)行功能測試,如安裝電子元件后的電路連通性、按鍵的靈敏度、接口的插拔性能等,驗證產(chǎn)品是否滿(mǎn)足設計要求和相關(guān)標準,避免因設計缺陷導致后期批量生產(chǎn)中出現的質(zhì)量問(wèn)題和售后問(wèn)題。
評估生產(chǎn)工藝:模擬批量生產(chǎn)的注塑工藝參數,評估手板模型的成型質(zhì)量,如是否有縮水、變形、翹曲等缺陷,為批量生產(chǎn)的工藝優(yōu)化提供參考依據,提前發(fā)現并解決可能出現的生產(chǎn)工藝問(wèn)題,降低生產(chǎn)成本和生產(chǎn)周期。
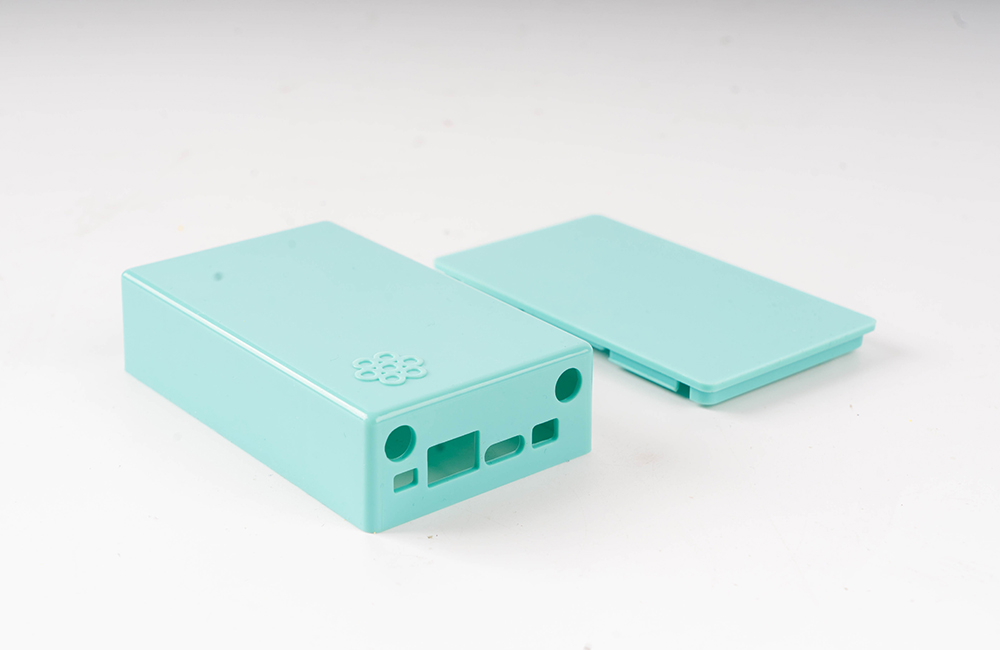
二、注塑加工電子設備外殼手板模型的制作流程
設計階段
三維建模:設計師使用專(zhuān)業(yè)的三維設計軟件,如SolidWorks、Pro/E、UG 等,根據電子設備的產(chǎn)品定位和設計要求,創(chuàng )建外殼的三維模型。在建模過(guò)程中,需要充分考慮產(chǎn)品的外觀(guān)美感、人體工程學(xué)、結構強度和裝配工藝等因素,確保設計的合理性和可行性。
模具設計:根據外殼的三維模型,設計注塑模具的結構。模具設計要考慮塑料的材料特性、收縮率、脫模方式、澆口位置和數量等因素,以確保能夠順利生產(chǎn)出高質(zhì)量的手板模型。模具通常由動(dòng)模和定模兩部分組成,通過(guò)合理的設計和制造,保證在注塑過(guò)程中塑料能夠均勻填充型腔,并在冷卻后易于脫模。
編程與仿真:將設計好的三維模型轉換為數控加工代碼,并進(jìn)行仿真分析。編程人員使用 Mastercam、PowerMILL 等編程軟件,根據模具的結構和加工工藝要求,生成數控機床能夠識別的 G 代碼和 M 代碼。通過(guò)仿真軟件,如 Vericut 等,對編程代碼進(jìn)行驗證和優(yōu)化,檢查刀具路徑是否合理、是否存在碰撞干涉等問(wèn)題,提高加工效率和質(zhì)量,減少機床故障和刀具損壞的風(fēng)險。
模具制作階段
材料選擇:根據模具的使用要求和成本預算,選擇合適的模具材料,如鋼材、鋁合金、銅合金等。鋼材具有較高的硬度和強度,適用于大規模生產(chǎn)的精密模具;鋁合金則具有較輕的重量和良好的導熱性能,適合制作小型、復雜形狀的模具或快速原型制作;銅合金具有良好的導電性和導熱性,常用于制作需要特殊散熱性能的模具。
CNC 加工:利用數控機床按照編程代碼對手板模型進(jìn)行加工。CNC 加工可以保證較高的加工精度和表面質(zhì)量,能夠準確地加工出模具的各個(gè)部件,包括型腔、型芯、滑塊、鑲件等。在加工過(guò)程中,需要嚴格控制加工參數,如切削速度、進(jìn)給量、切削深度等,以確保加工精度和表面粗糙度符合要求。
手工打磨與拋光:對 CNC 加工后的模具部件進(jìn)行手工打磨和拋光處理,去除加工刀痕和毛刺,提高模具的表面光潔度和尺寸精度。手工打磨可以使用砂紙、銼刀、研磨膏等工具,從粗到精逐步進(jìn)行打磨,使模具表面達到光滑平整的效果。拋光則可以進(jìn)一步提高模具表面的光澤度和外觀(guān)質(zhì)量,常用的拋光方法有機械拋光、化學(xué)拋光、電拋光等。
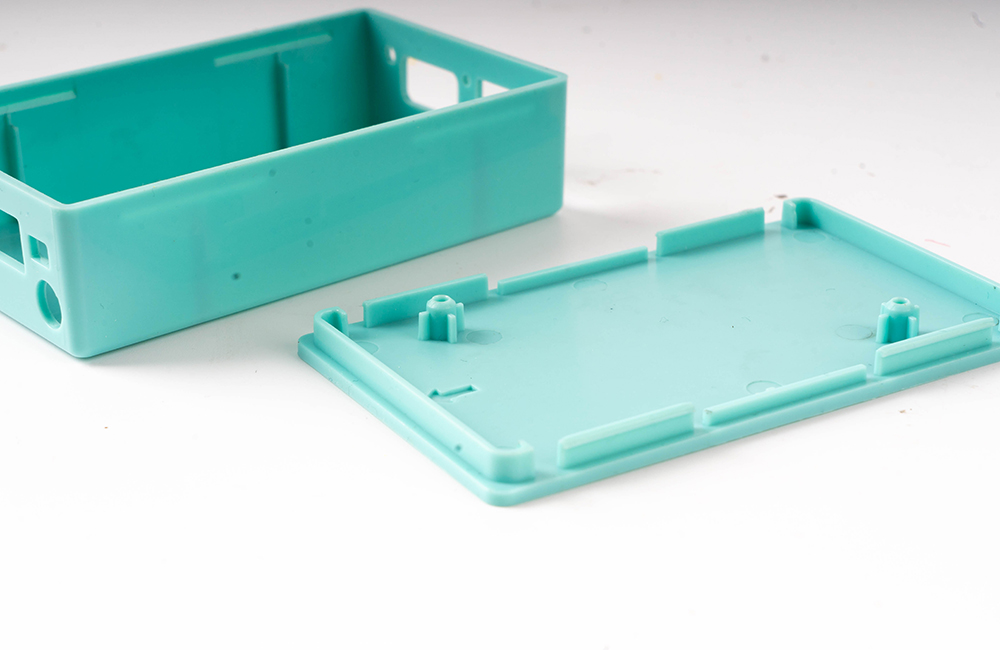
注塑成型階段
材料準備:選擇合適的塑料原料,如 ABS、PC、PMMA 等,并根據材料的干燥要求進(jìn)行預處理。塑料原料在使用前需要進(jìn)行干燥處理,以去除水分和揮發(fā)物,防止在注塑過(guò)程中產(chǎn)生氣泡、銀紋等缺陷。干燥的方式通常有自然干燥、烘箱干燥、真空干燥等,根據材料的性質(zhì)和含水量選擇合適的干燥方法和條件。
注塑參數設置:根據塑料材料的特性和手板模型的要求,設置注塑機的參數,如料筒溫度、模具溫度、注射壓力、保壓壓力、注射時(shí)間、冷卻時(shí)間等。這些參數的設置直接影響到手板模型的成型質(zhì)量和外觀(guān)效果,需要通過(guò)試驗和調試來(lái)確定最佳的參數組合。一般來(lái)說(shuō),料筒溫度應保證塑料能夠充分熔化和均勻混合,模具溫度應控制在一定范圍內,以保證塑料的充模能力和冷卻速度適中。
注塑成型:將干燥好的塑料原料加入注塑機的料筒中,經(jīng)過(guò)加熱熔化后,在注射裝置的作用下,將熔融的塑料注入模具型腔中。塑料在型腔中冷卻固化后,開(kāi)模取出手板模型。在注塑過(guò)程中,需要注意觀(guān)察產(chǎn)品的成型情況,及時(shí)調整注塑參數,避免出現缺料、燒焦、溢料等缺陷。
后處理階段
修剪與打磨:對手板模型進(jìn)行修剪和打磨處理,去除多余的飛邊、毛刺和澆口痕跡,使產(chǎn)品的邊緣光滑整齊。修剪可以使用剪刀、刀具等工具進(jìn)行,打磨則可以使用砂紙、銼刀、研磨機等設備,根據產(chǎn)品的表面要求和精度要求選擇合適的工具和方法進(jìn)行打磨。
裝配與測試:將經(jīng)過(guò)后處理的手板模型進(jìn)行裝配,安裝電子元件和其他配件,進(jìn)行功能測試和外觀(guān)檢查。在裝配過(guò)程中,需要確保各個(gè)部件之間的裝配精度和連接強度,避免出現松動(dòng)、卡滯等問(wèn)題。功能測試包括電氣性能測試、機械性能測試、環(huán)境適應性測試等,確保手板模型能夠滿(mǎn)足設計要求和使用標準。
表面處理:根據客戶(hù)的需求和產(chǎn)品的設計要求,對手板模型進(jìn)行表面處理,如噴漆、絲印、電鍍、燙金等,以提高產(chǎn)品的外觀(guān)效果和防護性能。表面處理可以使產(chǎn)品具有不同的顏色、光澤度和紋理效果,增強產(chǎn)品的美觀(guān)度和辨識度。
綜上所述,注塑加工電子設備外殼手板模型是一個(gè)集設計、加工、測試于一體的綜合過(guò)程。通過(guò)這一過(guò)程,可以有效地驗證產(chǎn)品設計的可行性,優(yōu)化生產(chǎn)工藝,提高產(chǎn)品質(zhì)量和市場(chǎng)競爭力。