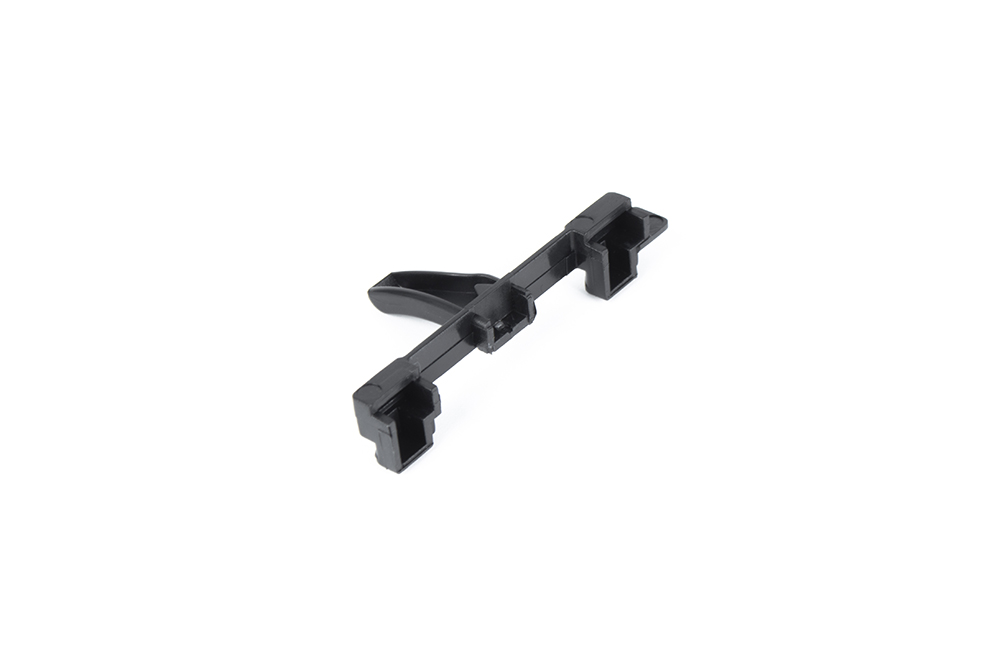
行業(yè)/分類(lèi):其他手板模型加工
加工方式: 注塑 使用材料: 塑料
最小精度: 0.1mm 生產(chǎn)周期: 2~7天
產(chǎn)品尺寸: 25cm*5cm*2cm
后處理: 噴油
注塑加工家電零件外殼手板模型是家電產(chǎn)品開(kāi)發(fā)過(guò)程中的重要環(huán)節,以下從設計、制作、成型、后處理到質(zhì)量檢測等方面進(jìn)行詳細介紹:
設計階段
產(chǎn)品設計:根據家電產(chǎn)品的功能需求、外觀(guān)要求及人機工程學(xué)原理,利用三維設計軟件如 SolidWorks、Pro/E 等進(jìn)行外殼手板模型的三維模型設計,確定外殼的整體結構、尺寸大小、按鍵位置、接口形式、散熱孔布局等細節。
圖紙繪制:將三維模型轉化為二維工程圖紙,標注出各個(gè)部位的尺寸、公差、表面粗糙度、裝配關(guān)系等技術(shù)要求,為后續的手板模型制作、模具設計和制造提供準確的指導。
手板模型制作
材料選擇:根據產(chǎn)品的性能要求、使用環(huán)境和預算,選擇合適的手板材料,如 ABS 具有良好的強度、易加工性和表面質(zhì)量;PC 抗沖擊性強、耐高溫;PP 耐磨損、抗酸堿等。
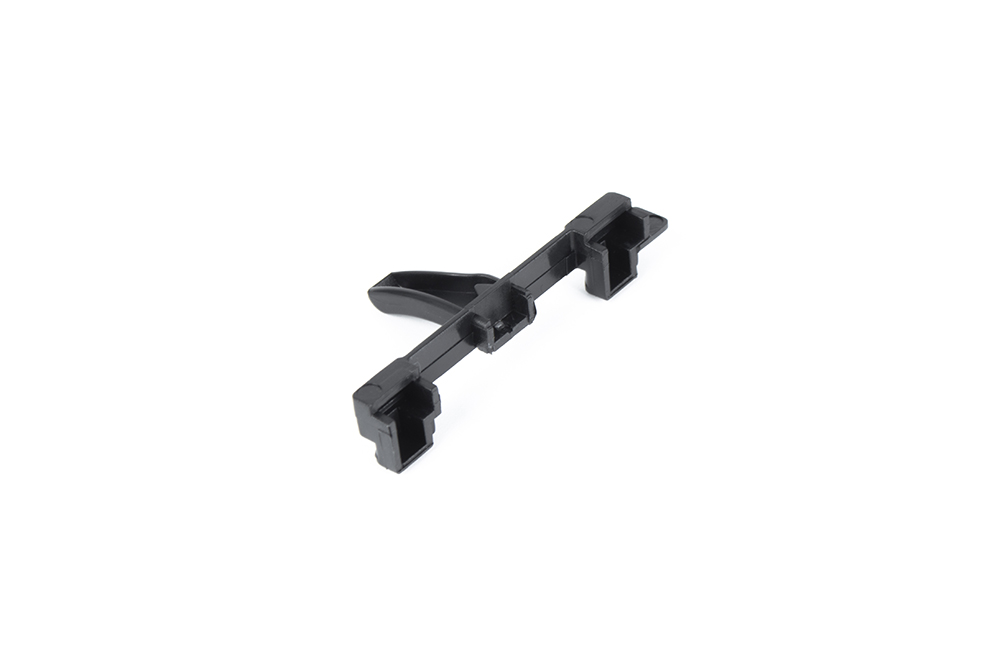
加工方式
CNC 加工:將三維模型文件導入 CNC 加工中心,通過(guò)銑削、鉆孔、磨削等工藝,從整塊材料上逐步去除多余部分,精確地加工出手板模型的外形,適合制作結構較為簡(jiǎn)單、精度要求高的手板。
3D 打印:采用 3D 打印技術(shù),根據三維模型數據,通過(guò)層層堆積材料的方式快速成型,制作出手板模型,適合制作結構復雜、具有精細細節的手板。
模具設計與制造
模具設計:根據手板模型和生產(chǎn)要求,設計注塑模具。確定模具的分型面、型腔數量、澆口位置、冷卻系統、頂出機構等結構,確保模具能夠順利成型產(chǎn)品,并保證產(chǎn)品的質(zhì)量和生產(chǎn)效率。
模具制造:選用合適的模具鋼材料,如 P20、H13 等,通過(guò) CNC 加工、電火花加工、線(xiàn)切割等工藝,精確地加工出模具的各個(gè)零部件。然后進(jìn)行模具的裝配和調試,確保模具的精度和性能符合要求。
注塑成型
注塑機調試:根據模具和材料的要求,調整注塑機的參數,包括注射壓力、注射速度、保壓壓力、保壓時(shí)間、冷卻時(shí)間等,以確保塑料能夠均勻地填充模具型腔,并獲得良好的成型質(zhì)量。
注塑生產(chǎn):將顆粒狀的塑料原料加入注塑機的料筒中,加熱熔化后,在注射壓力的作用下,將熔融塑料注入模具型腔中。經(jīng)過(guò)冷卻定型后,打開(kāi)模具,取出成型的家電零件外殼。
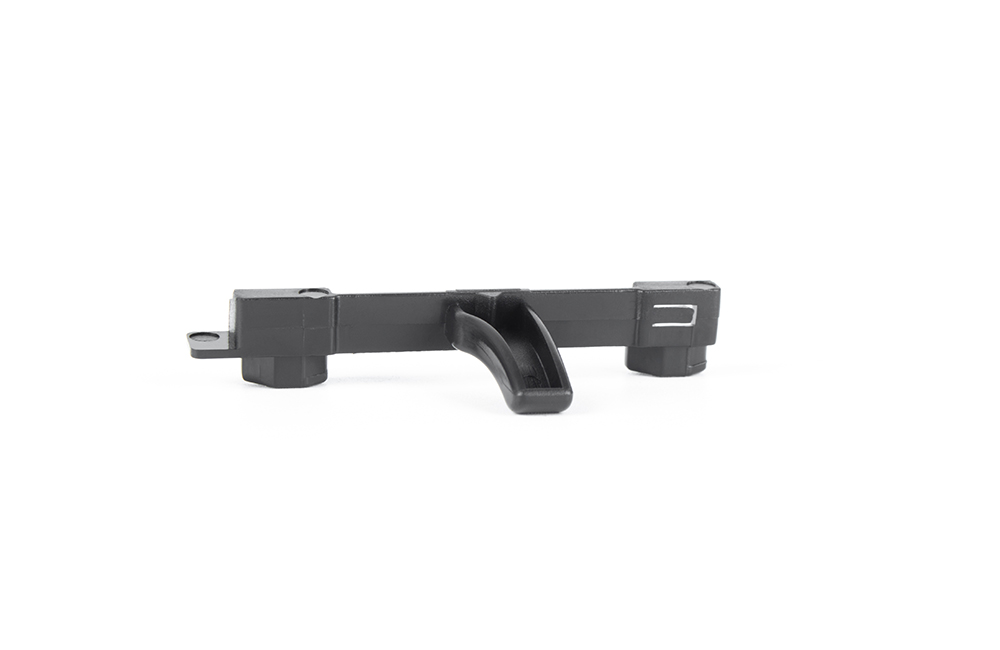
后處理
去毛刺與修邊:使用砂紙、銼刀等工具去除外殼上的飛邊、毛刺等,使外殼的邊緣光滑整潔,提高產(chǎn)品的外觀(guān)質(zhì)量和安全性。
表面處理:根據產(chǎn)品的需求,對注塑成型的外殼進(jìn)行表面處理,如噴漆、絲印、電鍍、拋光、磨砂等,以提升產(chǎn)品的美觀(guān)度、耐磨性、耐腐蝕性等性能。
質(zhì)量檢測
外觀(guān)檢查:檢查外殼的表面質(zhì)量,查看是否有飛邊、毛刺、缺料、氣泡、變形、色差等缺陷,確保外觀(guān)符合設計要求。
尺寸測量:使用量具如卡尺、千分尺、三坐標測量?jì)x等,測量外殼的關(guān)鍵尺寸,確保尺寸偏差在設計要求的公差范圍內。
裝配測試:將外殼與其他相關(guān)零部件進(jìn)行裝配,檢查裝配的順暢性和配合精度,確保各個(gè)零部件之間能夠正確裝配,形成完整的家電產(chǎn)品。
功能測試:對裝配好的家電產(chǎn)品進(jìn)行功能測試,模擬實(shí)際使用場(chǎng)景,檢測產(chǎn)品的各項功能是否正常,如按鍵是否靈敏、接口是否有效、散熱是否良好等。